Revolutionizing Motion Control The Power of Hysteresis Technology in Modern Industries
In the ever-evolving landscape of industrial automation and precision engineering, the demand for reliable, efficient, and adaptable motion control solutions has never been higher. Among the unsung heroes of this domain are hysteresis-based devices—hysteresis brakes, hysteresis dynamometers, hysteresis clutches, and their integration into advanced motor test systems. These technologies form the backbone of countless applications, from automotive R\u0026D to renewable energy systems, offering unparalleled accuracy and durability. Let’s explore how these innovations are transforming industries and why they deserve a spotlight in your next project.
The Science Behind Hysteresis: A Foundation for Precision
At the heart of hysteresis technology lies a simple yet profound principle: the conversion of kinetic energy into heat through magnetic hysteresis loss. Unlike friction-based systems that rely on physical contact, hysteresis devices use magnetic fields to generate torque or resistance. This non-contact operation eliminates wear, reduces maintenance, and ensures consistent performance over time. Whether it’s controlling speed in a high-speed motor or simulating real-world load conditions in a dynamometer, hysteresis-based systems deliver results without compromise.
Hysteresis Brakes: Silent Guardians of Controlled Motion
Hysteresis brakes are indispensable in applications requiring smooth, adjustable torque without mechanical wear. Their ability to provide precise braking force makes them ideal for tension control in packaging machinery, web handling in printing, and even robotics. For instance, in semiconductor manufacturing, where micron-level precision is critical, hysteresis brakes ensure delicate materials are handled without slippage or damage. Their silent operation and maintenance-free design also make them a favorite in noise-sensitive environments like medical imaging devices.
Torque sensors for automation : The Ultimate Test Partners
When it comes to testing motors, turbines, or powertrains, hysteresis dynamometers are the gold standard. These devices simulate real-world loads with exceptional accuracy, enabling engineers to validate performance under diverse conditions. A motor test system equipped with a hysteresis dynamometer can replicate everything from sudden torque spikes in electric vehicles to steady-state loads in industrial pumps. This capability is crucial for industries like aerospace, where every component must withstand extreme stresses before deployment.
Hysteresis Clutches: Bridging Efficiency and Control
Hysteresis clutches excel in applications requiring slip control and torque regulation. In conveyor systems, for example, they prevent overloads by allowing controlled slippage during jams, protecting both machinery and products. Renewable energy systems, such as wind turbines, use these clutches to manage variable torque from fluctuating wind speeds, ensuring stable power output. Their ability to operate at high speeds without degradation makes them a versatile solution for hybrid vehicles and precision manufacturing lines.
Motor Test Systems: Where Innovation Meets Validation
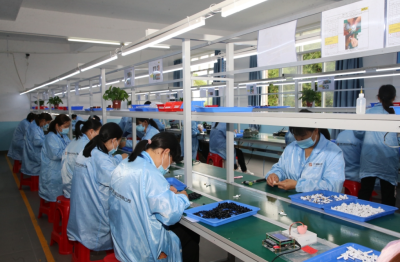
Modern motor test equipment is more than just a diagnostic tool—it’s a gateway to innovation. A comprehensive motor test system integrates hysteresis dynamometers, data acquisition modules, and advanced software to provide a 360-degree view of motor performance. For electric vehicle manufacturers, such systems are vital for optimizing efficiency, extending battery life, and meeting stringent regulatory standards. In the realm of industrial automation, they ensure motors operate within specified parameters, reducing downtime and energy costs.
Applications Across Industries: From Concept to Reality
The versatility of hysteresis-based devices spans multiple sectors. In automotive testing, hysteresis dynamometers are used to evaluate hybrid and electric drivetrains under simulated road conditions. Aerospace engineers rely on them to test aircraft actuators and landing gear systems. Even the renewable energy sector benefits—wind turbine manufacturers use hysteresis brakes to control blade pitch during storms, while solar tracking systems employ hysteresis clutches to adjust panel angles with precision.
Future Trends: Smarter, Faster, Greener
As industries push toward sustainability and smart manufacturing, hysteresis technology is evolving to meet new challenges. Next-gen motor test systems now incorporate AI-driven analytics to predict failures before they occur. Hysteresis brakes and clutches are being redesigned with lightweight materials for use in drones and electric aviation. Moreover, the shift toward Industry 4.0 has spurred demand for IoT-enabled hysteresis devices that communicate seamlessly with centralized control systems, enabling real-time adjustments and remote monitoring.
Choosing the Right Partner: What to Look For
Selecting the right hysteresis-based equipment hinges on understanding your specific needs. For motor testing, prioritize dynamometers with high-speed data sampling and customizable load profiles. In automation, opt for hysteresis brakes with zero-backlash designs for repeatable accuracy. Partnering with suppliers who offer end-to-end support—from system design to calibration—ensures seamless integration into your workflows.
Conclusion: Elevate Your Engineering with Hysteresis Innovation
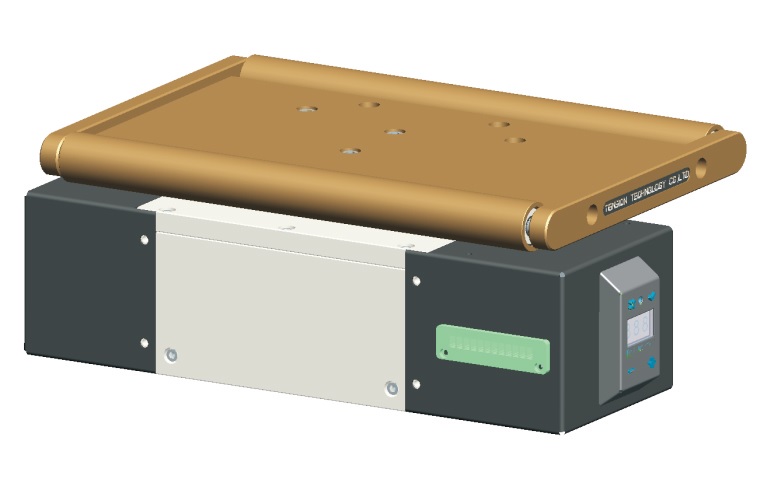
In a world where precision and reliability are non-negotiable, hysteresis brakes, dynamometers, and clutches stand as pillars of modern engineering. Their ability to deliver consistent performance, reduce downtime, and adapt to diverse applications makes them indispensable tools for innovators. Whether you’re refining an electric motor’s efficiency or safeguarding a production line from overloads, hysteresis technology offers solutions that are as durable as they are dynamic.
As industries continue to embrace automation and sustainability, the role of advanced motor test systems will only grow. By integrating hysteresis-based devices into your operations today, you’re not just solving current challenges—you’re future-proofing your success. The question isn’t whether you need these technologies, but how quickly you can harness their potential to outpace the competition.
---
This article highlights the transformative impact of hysteresis technology while maintaining a human-centric narrative, avoiding technical jargon overload. It balances practical examples with forward-looking insights to engage both technical and managerial audiences.